Gree Mini Split Troubleshooting Guide.
Gree Mini Split Troubleshooting guide will help you operate and handle your Gree mini split effectively.Gree mini split system is efficient and versatile solution for heating and cooling individual rooms or zones within a building.
This innovative HVAC (Heating, Ventilation, and Air Conditioning) system consists of two main components: an outdoor unit and one or more indoor air-handling units.
What sets Gree mini-splits apart is their exceptional energy efficiency, quiet operation, and flexibility.
Also read>>>>Disadvantages Of Mini Split Systems.
The outdoor unit contains a compressor and is responsible for expelling or absorbing heat, depending on the mode (heating or cooling).
The indoor unit, typically mounted on a wall or ceiling, disperses the conditioned air into the room. Gree mini-splits use a refrigerant cycle to transfer heat, making them highly efficient and environmentally friendly.
One of the key benefits of Gree mini-splits is their zoning capability. You can independently control the temperature of different rooms or zones, saving energy by only conditioning spaces that are in use.
Additionally, Gree systems often come with advanced features like inverter technology, which allows for precise temperature control and reduced energy consumption.
With a reputation for reliability and innovation, Gree mini-splits are an excellent choice for homes, offices, or any space where personalized climate control and energy efficiency are essential.
Their user-friendly controls and sleek design make them a popular choice for those seeking both comfort and style in their HVAC systems.
Also read>>>>Smallest Mini Split.
Troubleshooting a Gree Mini Split system may be necessary due to various issues.
Here are the top four common problems that might require attention:
- Lack of Cooling or Heating: If the system isn’t providing the desired temperature, it could be due to issues with the compressor, refrigerant levels, or air filters.
- Airflow Problems: Poor airflow could result from a clogged filter, obstructed vents, or issues with the fan motor, reducing the system’s efficiency.
- Water Leaks: Water leaks from the indoor or outdoor unit may indicate a blockage in the drain line or a refrigerant leak, which should be addressed promptly.
- Strange Noises: Unusual sounds like grinding, hissing, or rattling can be a sign of loose components, malfunctioning fans, or other mechanical issues that require investigation.
Identifying and addressing these problems promptly can help maintain the efficiency and longevity of your Gree Mini Split system, ensuring that it continues to provide comfortable, energy-efficient heating and cooling for your space.
Also read: Emerson Thermostat Troubleshooting
Gree Mini Split Troubleshooting.
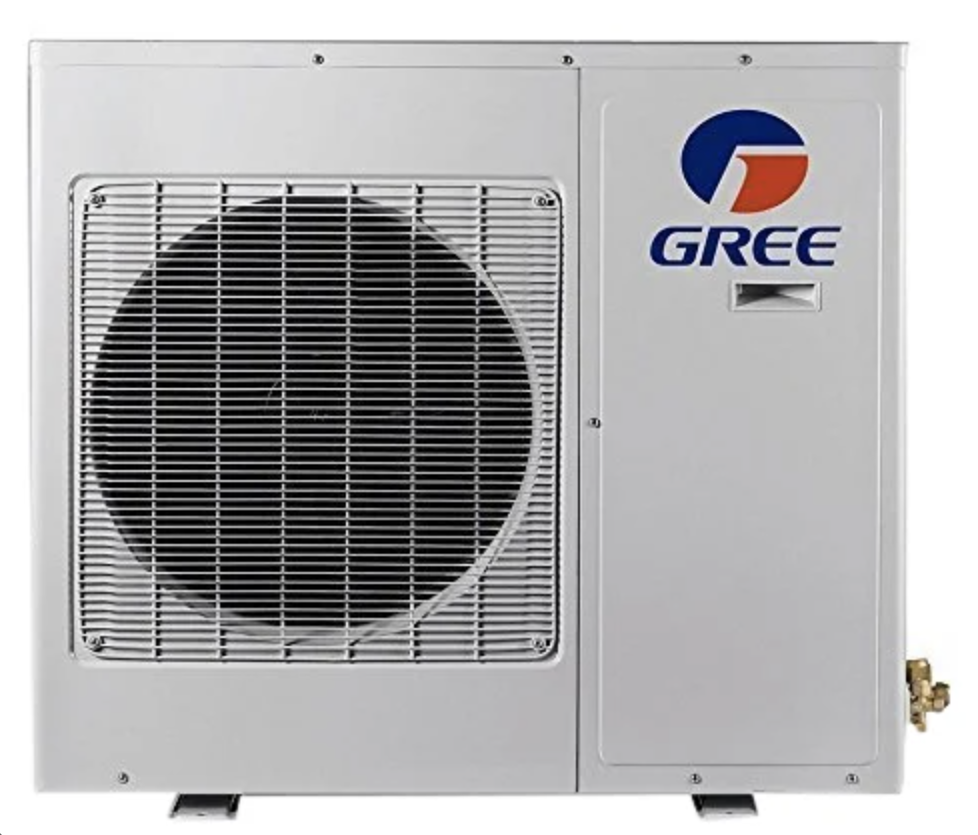
1.Onboard Diagnostics.
Onboard diagnostics, often referred to as OBD, is a valuable troubleshooting method for Gree Mini-Split systems, just as it is in automotive applications.
This approach involves the use of built-in diagnostic tools and error codes to identify and resolve issues efficiently.
*Error Codes and Display Panel:
Gree Mini-Split systems typically come with a digital display panel on the indoor unit.
When an issue arises, the system may display an error code. These codes provide valuable information for troubleshooting.
*Understanding the Error Codes:
Gree Mini-Split systems have a specific set of error codes, each corresponding to different problems.
These codes are typically outlined in the user manual or service documentation.
*Interpreting Common Error Codes:
“E1” might indicate an issue with the sensor or temperature control.
“E2” could signal a problem with the indoor or outdoor unit’s communication.
“E3” often relates to faults in the system’s refrigerant.
*Diagnostic Procedures:
When an error code is displayed, users or technicians can follow the diagnostic procedures outlined in the manual.
These procedures guide users through steps to identify the root cause of the problem.
*Maintenance and Repairs:
Depending on the diagnosis, maintenance or repair tasks can be initiated.
These might include cleaning air filters, checking refrigerant levels, or servicing components.
*Professional Assistance:
For complex issues or those requiring specialized tools, it’s advisable to seek assistance from a trained technician.
Also read>>>>Common Problems with PTAC Units.
2.IDU/ODU Sensor and Mainboard Diagnostics.
IDU (Indoor Unit) and ODU (Outdoor Unit) sensor and mainboard diagnostics are crucial troubleshooting methods for Gree Mini-Split systems, enabling users to identify and address issues related to these components.
*Understanding the Components:
Gree Mini-Split systems consist of both an indoor unit (IDU) and an outdoor unit (ODU).
These units are equipped with various sensors and mainboards responsible for system operation and communication.
*Identifying Sensor Issues:
If you encounter problems with the IDU or ODU, such as irregular temperature or performance, sensor diagnostics come into play.
Sensors in the IDU monitor factors like room temperature and humidity, while those in the ODU track outdoor conditions.
*Using Diagnostic Codes:
Gree Mini-Split systems may display error codes related to sensor malfunctions on the control panel or via a remote control.
Consult the user manual or service documentation to decode these error codes.
*Diagnostic Procedures:
When an error code suggests a sensor issue, users can follow prescribed diagnostic procedures.
This might involve inspecting sensors, checking wiring connections, and verifying sensor readings.
*Mainboard and Communication Diagnostics:
Issues in communication between the IDU and ODU or problems with the mainboard can lead to system malfunctions.
Diagnostic codes specific to these issues may be displayed.
*Inspecting Wiring and Connections:
Users or technicians can visually inspect wiring and connections between the mainboard, sensors, and the control board.
Loose or damaged connections can often be the source of communication issues.
*Replacement and Repairs:
If sensor or mainboard issues persist, replacement or repair of the affected components may be necessary.
Professional assistance might be required for complex repairs.
*Regular Maintenance:
To prevent sensor and mainboard issues, regular maintenance of the Gree Mini-Split system is essential. This includes cleaning filters and ensuring proper airflow.
3.EEV Diagnostics.
EEV diagnostics are essential for troubleshooting Gree Mini-Split systems, particularly when issues are related to the electronic expansion valve.
The EEV is a critical component responsible for regulating refrigerant flow in the system, and diagnosing its performance is crucial.
*Understanding the Electronic Expansion Valve (EEV):
The EEV is responsible for controlling the flow of refrigerant within the Gree Mini-Split system.
It adjusts the refrigerant flow rate to match the cooling or heating demand, ensuring efficient operation.
*Symptoms of EEV Issues:
Common symptoms of EEV problems may include insufficient cooling or heating, irregular temperature control, or unusual noises.
Recognizing these symptoms is the first step in diagnosing potential EEV issues.
*Diagnostic Codes and Display:
Gree Mini-Split systems often use error codes to indicate problems, including those related to the EEV.
Error codes associated with EEV issues may be displayed on the control panel or via a remote control.
*Interpreting Error Codes:
Consult the system’s user manual or service documentation to decode specific EEV-related error codes.
Error codes help identify the nature of the problem, such as a valve malfunction or sensor issue.
*Diagnostic Procedures:
Upon receiving an EEV-related error code, users can follow the prescribed diagnostic procedures provided in the manual.
These procedures may involve checking EEV wiring, sensor connections, and inspecting the valve itself.
*Measuring Valve Performance:
In some cases, technicians may use specialized diagnostic tools to measure the EEV’s performance, including valve opening and closing times.
Deviations from optimal performance can indicate the need for adjustments or valve replacement.
4.Compressor diagnostics.
Compressor diagnostics are crucial for identifying and addressing issues related to the compressor in a Gree Mini-Split system.
The compressor is a vital component responsible for cooling or heating, and diagnosing its performance is essential.
*Understanding the Compressor:
The compressor in a Gree Mini-Split system pressurizes the refrigerant, facilitating heat exchange and temperature control.
It plays a central role in the system’s cooling and heating functions.
*Symptoms of Compressor Issues:
Common symptoms of compressor problems may include inadequate cooling or heating, unusual noises (e.g., knocking or clicking), or frequent system cycling.
Recognizing these symptoms is the first step in diagnosing potential compressor issues.
*Diagnostic Codes and Display:
Gree Mini-Split systems often use error codes to indicate problems, including those related to the compressor.
Error codes associated with compressor issues may be displayed on the control panel or via a remote control.
*Interpreting Error Codes:
Consult the system’s user manual or service documentation to decode specific compressor-related error codes.
Error codes help identify the nature of the problem, such as compressor overheating or electrical faults.
*Diagnostic Procedures:
Upon receiving a compressor-related error code, users can follow the prescribed diagnostic procedures provided in the manual.
These procedures may involve checking electrical connections, inspecting refrigerant lines, and assessing the compressor’s condition.
*Measuring Compressor Performance:
Technicians may use specialized diagnostic tools to measure the compressor’s performance, such as pressure and temperature readings.
Deviations from optimal performance can indicate the need for adjustments or compressor replacement.
*Refrigerant Level Inspection:
An imbalanced or low refrigerant level can strain the compressor. Ensure that refrigerant levels are within the recommended range.
Also read>>>>Goodman Air Conditioner Problems.
5.IDU fan motor diagnostics.
Diagnostics related to the Indoor Unit (IDU) fan motor are vital for identifying and resolving issues that might affect the performance of a Gree Mini-Split system.
The IDU fan motor is responsible for the circulation of conditioned air within the room. Here’s an educative breakdown of this troubleshooting method:
*Understanding the IDU Fan Motor:
The IDU fan motor plays a crucial role in distributing conditioned air in the room.
It assists in maintaining temperature and airflow consistency.
*Symptoms of IDU Fan Motor Issues:
Common symptoms of IDU fan motor problems may include reduced or no airflow, inconsistent temperature, or unusual noises (e.g., squeaking or grinding).
Recognizing these symptoms is the first step in diagnosing potential fan motor issues.
*Diagnostic Codes and Display:
Gree Mini-Split systems often use error codes to indicate problems, including those related to the fan motor.
Error codes associated with fan motor issues may be displayed on the control panel or via a remote control.
*Interpreting Error Codes:
Consult the system’s user manual or service documentation to decode specific fan motor-related error codes.
Error codes help identify the nature of the problem, such as motor malfunction or electrical issues.
*Diagnostic Procedures:
Upon receiving a fan motor-related error code, users can follow the prescribed diagnostic procedures provided in the manual.
These procedures may involve inspecting the fan motor, checking electrical connections, and verifying proper motor operation.
*Fan Blade and Housing Inspection:
Visual inspection of the fan blades and housing is essential. Obstructions, dirt, or damage to these components can impede airflow and motor performance.
*Motor Lubrication:
Some fan motors require periodic lubrication. Check the user manual for guidance on lubrication intervals and procedures.
6.Reactor / PFC Inductance.
Diagnostics related to Reactor/PFC (Power Factor Correction) Inductance components in a Gree Mini-Split system are essential for maintaining electrical efficiency and system performance. These components help manage the power quality of the system.
*Understanding Reactor/PFC Inductance:
Reactors and PFC inductors are electrical components designed to improve power quality by correcting the power factor of the system.
These components help reduce electrical noise and improve energy efficiency.
*Symptoms of Reactor/PFC Inductance Issues:
Common symptoms of reactor/PFC inductance problems may include voltage fluctuations, electrical surges, or decreased system efficiency.
Recognizing these symptoms is the first step in diagnosing potential issues.
*Diagnostic Codes and Display:
Some Gree Mini-Split systems use error codes to indicate electrical problems, including those related to reactor/PFC inductance.
Error codes associated with these issues may be displayed on the control panel or via a remote control.
*Interpreting Error Codes:
Consult the system’s user manual or service documentation to decode specific reactor/PFC inductance-related error codes.
Error codes help identify the nature of the electrical problem, such as inductor failure or wiring issues.
*Diagnostic Procedures:
Upon receiving an error code related to reactor/PFC inductance, users can follow the prescribed diagnostic procedures provided in the manual.
These procedures may involve inspecting inductors, checking wiring connections, and testing their performance.
*Electrical Circuit Inspection:
Visual inspection of the electrical circuit connected to the inductors is crucial. Loose or damaged connections can lead to power quality issues.
*Inductor Replacement:
If testing indicates inductor failure, replacement is necessary. It’s recommended to use the manufacturer’s specified components for compatibility.
7.GREE diagnostic tools.
GREE diagnostic tools are specialized equipment and software designed to facilitate the troubleshooting and maintenance of Gree Mini-Split systems.
These tools provide advanced capabilities for identifying and resolving system issues.
*Understanding GREE Diagnostic Tools:
GREE diagnostic tools are specifically designed for use with Gree Mini-Split systems and are developed by the manufacturer for efficient system diagnostics.
*Advanced System Diagnostics:
GREE diagnostic tools offer advanced diagnostic features that go beyond standard error codes.
They can access detailed system information, monitor various parameters, and perform in-depth system analysis.
*Symptoms of System Issues:
To utilize GREE diagnostic tools, technicians first identify symptoms and issues within the Gree Mini-Split system.
These symptoms can range from temperature irregularities to strange noises or other performance problems.
*Connecting the Diagnostic Tool:
GREE diagnostic tools are typically connected to the Mini-Split system’s control panel, data port, or communication interface.
They establish communication with the system for real-time monitoring.
*Data Retrieval and Analysis:
The tool retrieves data related to the system’s operation, including sensor readings, temperature, electrical parameters, and error logs.
This data is analyzed to pinpoint the root cause of the issue.
*Error Code Interpretation:
The diagnostic tool can interpret error codes and provide detailed information about the specific fault, making it easier to diagnose problems.
*Advanced Functionality:
GREE diagnostic tools often offer additional functions like adjusting system parameters, performing firmware updates, or calibrating sensors.
*Recommendations and Repairs:
Based on the analysis, the tool may provide recommendations for repairs, part replacements, or system adjustments.
Technicians can then perform the necessary tasks to address the issues.
*Training and Expertise:
Proper utilization of GREE diagnostic tools often requires training and expertise.
Technicians should be well-versed in system diagnostics and the use of these specialized tools.
*Efficiency and Precision:
The use of GREE diagnostic tools significantly enhances troubleshooting efficiency, reduces downtime, and ensures precise identification of system issues.
Frequently Asked Questions (FAQs)
What should I do if my Gree Mini-Split system is not cooling or heating as expected?
If your system is not performing adequately, it’s essential to check for error codes on the control panel or remote control.
Refer to the user manual to decode the specific error code and follow the diagnostic procedures outlined to identify the issue.
Common problems may include issues with sensors, refrigerant levels, or airflow, and addressing these can help restore the system’s performance.
My Gree Mini-Split system is making strange noises. What should I do?
Unusual noises, such as squeaking, grinding, or clicking, can indicate potential issues. Start by checking the system for error codes.
If you find an error related to the fan motor or compressor, follow the diagnostic procedures provided in the manual.
Inspect fan blades, housing, and electrical connections. For compressor issues, inspect electrical connections, wiring, and refrigerant levels.
How can I identify electrical problems in my Gree Mini-Split system, and what should I do about them?
Electrical issues may manifest as voltage fluctuations, surges, or decreased efficiency. If you observe abnormal electrical behavior, consult the system’s error codes.
If you encounter an error code related to electrical components, refer to the user manual for guidance.
Visual inspections of wiring, connections, and inductors are essential. For advanced diagnostics and adjustments, professional assistance may be necessary.
What are the advantages of using GREE diagnostic tools for troubleshooting my Gree Mini-Split system?
GREE diagnostic tools offer advanced capabilities for precise system diagnostics beyond standard error codes.
They can access detailed system information, monitor various parameters, and perform in-depth analysis.
These tools are designed for efficient and accurate issue identification. They can interpret error codes, provide detailed fault information, and even offer recommendations for repairs, making them a valuable asset for technicians working with Gree Mini-Split systems.
Proper training and expertise are essential for using these tools effectively.
Conclusion.
Troubleshooting a Gree Mini-Split system involves a systematic approach, with various methods and diagnostic tools at your disposal.
Whether it’s interpreting error codes, diagnosing components like the compressor, fan motor, or reactor/PFC inductance, or leveraging specialized GREE diagnostic tools, a thorough understanding of the system’s operation is vital.
Regular maintenance, visual inspections, and addressing issues promptly are key to ensuring the efficiency and longevity of your Gree Mini-Split.
By recognizing symptoms, interpreting error codes, and following recommended diagnostic procedures, users can take a proactive role in maintaining the optimal performance of their HVAC systems while seeking professional assistance when needed.